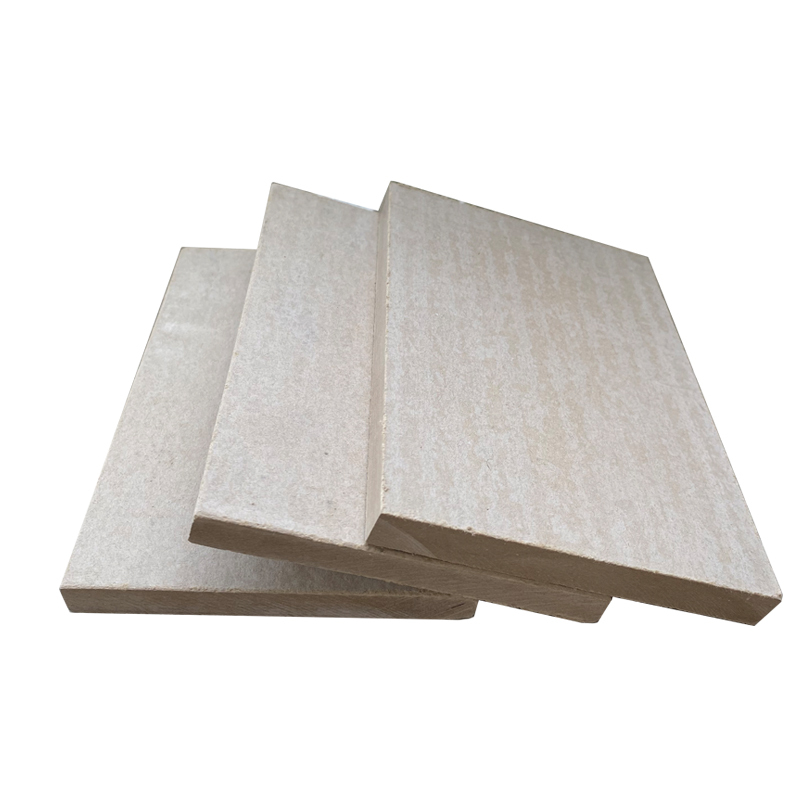
How Does the Thickness of the Calcium Silicate Board Affect Its Strength and Performance?
Calcium silicate board is a widely used construction material due to its high strength, durability, and fire resistance properties. It is made from a combination of cement, silica, and cellulose fibers, which are processed to form a rigid board. The thickness of the calcium silicate board plays an important role in determining its strength and performance.
Strength and Load Capacity
The thickness of the calcium silicate board is directly proportional to its strength and load capacity. The thicker the board, the higher it's compressive strength and load-carrying capacity. Thicker boards are able to withstand more weight and stress without breaking or deforming.
Flexibility and Bend Strength
The thickness of the calcium silicate board affects its flexibility and bend strength. Thicker boards are less flexible and more rigid, which makes them less prone to bending or warping under stress.
On the other hand, thinner boards are more flexible and have higher bend strength, which makes them more suitable for applications where they will be exposed to bending or flexing.
Thermal Insulation
The thickness of the calcium silicate board affects its thermal insulation properties. Thicker boards have higher insulation values and are better at retaining heat than thinner boards. It makes them ideal for use in applications where heat retention is important, such as in furnaces, kilns, and other high-temperature environments.
Sound Insulation
Thicker boards have higher sound insulation values and are better at blocking noise than thinner boards. This makes them ideal for use in applications where noise reduction is important, such as in walls, floors, and ceilings.
Other Factors Affecting the Performance of Calcium Silicate Board
While thickness is an important factor in determining the strength and performance of calcium silicate board, there are other factors that should also be considered.
For example, the quality of the raw materials used in the manufacturing process, as well as the manufacturing process itself, can also affect the strength and performance of the board. Additionally, the design and installation of the board can impact its performance and longevity.
Environmental factors should also be taken into consideration. Calcium silicate board is known for its resistance to fire, moisture, and mold, but exposure to harsh environmental conditions can still impact its performance. Factors such as temperature, humidity, and exposure to chemicals can all affect the strength and durability of the board.
Maintenance is also an important consideration. Regular inspections and maintenance can help identify any issues with the board before they become more serious. Repairs and replacements should be done promptly to ensure the board continues to perform optimally.
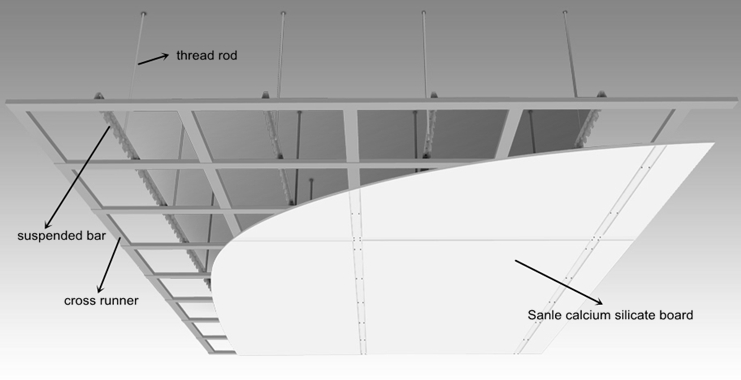
Applications of Calcium Silicate Board
Calcium silicate board has a wide range of applications in the construction industry, including in walls, ceilings, floors, and roofs. It is also used in industrial applications such as in furnaces, kilns, and power plants. Some other applications include:
● Fireproofing: A calcium silicate board is a popular choice for fireproofing due to its ability to withstand high temperatures and its resistance to flames and smoke.
● Insulation: The thermal and sound insulation properties of calcium silicate board make it an ideal choice for insulation in buildings and industrial applications.
● Cladding: Calcium silicate board can be used as a decorative cladding material for buildings, providing both aesthetic and functional benefits.
● Structural Support: Thicker calcium silicate board can be used as a structural support material in buildings and other structures.
Conclusion
The thickness of the calcium silicate board plays a crucial role in determining its strength and performance. When selecting a board for a specific application, it is important to consider factors such as load capacity, flexibility, thermal insulation, and sound insulation requirements.
Additionally, the quality of raw materials, manufacturing process, design and installation, environmental factors, and maintenance should also be taken into consideration.
Calcium silicate board has a wide range of applications in the construction and industrial sectors, and selecting the appropriate thickness provides the desired benefits for your specific application.